Introduction
The rotor fan in a handheld electric planer plays a crucial role in cooling the motor and ensuring efficient operation. Similarly, an angle grinder’s rotor is an essential component responsible for driving the abrasive wheel at high speeds. Given that both tools operate with high-speed rotating components, a question arises: can a rotor fan from a handheld electric planer be used on an angle grinder rotor? This article explores the feasibility, compatibility, potential modifications, and risks associated with such an interchange.
Structural and Functional Differences
Handheld electric planers and angle grinders are designed for distinct purposes, which directly impacts the design of their rotors and cooling mechanisms.
Handheld Electric Planer Rotor Fan
- Purpose: The rotor fan in a planer is primarily designed to dissipate heat generated during prolonged operation. It ensures that the internal components do not overheat, thereby extending the motor’s lifespan.
- Design: Typically made of plastic or lightweight metal, the fan is aerodynamically structured to create a strong airflow within the housing.
- Rotation Speed: Handheld electric planers operate at relatively moderate speeds compared to angle grinders, influencing the fan’s structural durability.
Angle Grinder Rotor and Cooling System
- Purpose: The rotor in an angle grinder is designed to provide high rotational speed to the grinding wheel while maintaining efficient cooling to prevent overheating.
- Design: The cooling system in an angle grinder generally includes vents and sometimes an integrated cooling fan.
- Rotation Speed: Angle grinders operate at extremely high RPMs, which places significant stress on all components, including any cooling fans.
Compatibility Analysis
Using a handheld electric planer rotor fan on an angle grinder rotor presents several challenges:
- Size and Fitment: The dimensions of the rotor fan must match the rotor shaft of the angle grinder. If the bore size or mounting system differs, modifications would be required.
- Material Strength: Given that angle grinders operate at higher RPMs, the rotor fan from a planer may not be structurally sufficient to withstand the forces generated during operation.
- Cooling Efficiency: Angle grinders typically generate more heat than planers due to their high-speed operation and heavy-duty applications. A planer’s fan may not provide adequate airflow to maintain optimal cooling.
- Vibration and Balance Issues: Any imbalance in the rotor assembly can lead to excessive vibration, which may damage the motor or reduce the tool’s lifespan.
Potential Modifications
If one were to attempt using a handheld electric planer rotor fan on an angle grinder, certain modifications would be necessary:
- Adjusting the Bore Size: If the planer fan does not fit the grinder’s rotor shaft, it may require machining or the use of adapters.
- Material Reinforcement: Strengthening the fan with metal or high-durability plastic may help it endure higher speeds.
- Balancing the Fan: Professional balancing equipment may be required to ensure that the modified fan does not introduce excessive vibration.
- Testing Under Load: After modifications, thorough testing must be conducted to verify that the fan can sustain operation without failing.
Risks and Drawbacks
Several risks are associated with attempting this interchange:
- Safety Hazards: If the fan breaks due to stress, high-speed fragments can cause injury.
- Reduced Performance: An improperly fitted fan may not cool the motor efficiently, leading to overheating and motor damage.
- Warranty Voidance: Modifying power tools often voids manufacturer warranties, which could be costly if damage occurs.
- Long-Term Durability Issues: The lifespan of the tool may be significantly reduced if the cooling system is not functioning optimally.
Alternative Solutions
Instead of attempting to adapt a planer rotor fan for an angle grinder, consider these alternatives:
- Using Manufacturer-Approved Parts: Original replacement fans designed specifically for the angle grinder ensure compatibility and safety.
- Custom Machining a New Fan: If a replacement fan is unavailable, custom fabrication using high-quality materials can be an option.
- Enhancing Cooling Through Additional Ventilation: Increasing airflow through improved housing vents or using external cooling methods may be more effective.
Additional Considerations
When dealing with power tool modifications, additional factors should be considered:
- Power and Torque Differences: The rotational forces in an angle grinder differ from those in a planer. The torque exerted on the rotor fan in a grinder is much higher, which could lead to premature failure if the fan is not designed to handle it.
- Thermal Resistance of Materials: Some planer fans may be made of materials that cannot endure the high heat levels of an angle grinder, causing them to deform or break apart.
- Aerodynamic Properties: The airflow generated by a planer fan may not align with the cooling needs of an angle grinder. Inadequate cooling could result in a thermal overload and eventual motor burnout.
- Manufacturer Specifications: Before modifying a power tool, consulting the manufacturer’s specifications is essential. Some tools have built-in safety mechanisms that could be compromised by modifications.
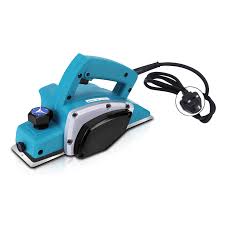
Real-World Testing and Case Studies
If an individual or professional workshop decides to test the feasibility of using a planer fan in an angle grinder, a structured testing approach should be followed:
- Initial Fitment Test: Ensuring that the fan can be securely attached to the angle grinder’s rotor.
- Low-Speed Operation Test: Running the modified grinder at a lower speed to check for any irregularities in balance and airflow.
- Thermal Imaging Analysis: Using a thermal camera to observe temperature differences before and after installation of the new fan.
- Durability Test: Running the tool under a heavy load to determine if the fan can sustain prolonged operation without breaking.
- Performance Benchmarking: Comparing motor efficiency, heat dissipation, and vibration levels between the modified tool and a stock angle grinder.
Expert Opinions
Many power tool engineers and professionals caution against using non-original components in high-speed tools. According to industry experts:
- Material engineers emphasize the importance of high-temperature-resistant plastics or metals in power tool fans.
- Tool repair specialists warn that improper balancing can lead to excessive wear on motor bearings, reducing the lifespan of the tool.
- Safety analysts highlight the potential dangers of fan failure at high RPMs, which could lead to accidents or damage to surrounding materials.
Conclusion
While a handheld electric planer rotor fan may physically be attached to an angle grinder rotor with modifications, it is not a recommended solution due to structural, safety, and functional concerns. Angle grinders operate at significantly higher speeds and generate more heat than planers, necessitating a cooling system specifically designed for such conditions. Instead of using an incompatible component, it is advisable to seek manufacturer-approved replacement parts or consider alternative cooling enhancements to ensure optimal performance and safety. Ultimately, ensuring the longevity and safe operation of power tools requires using components specifically engineered for their intended application.